Are robots the future ?
A robot can be the answer to many industrial challenges, but is not always the best option. Robots may, for example, not be ideal for high speed packaging lines of standard products such as a filling lines running at 72,000 bottles per hour. It can be better to provide these lines with standard systems developed specifically for them, which, although less flexible, are more adaptable and take less space than robots.
The implementation of robotic solutions can have a positive impact on other types of packaging lines, bringing undeniable gains in terms of profitability, flexibility, performance and product quality.
Robots can save your company
Many organizations are constrained to more flexibility. To satisfy their customers, they must constantly adapt the characteristics of their products and their packaging. They are pressured
to produce smaller orders forcing them to make more frequent format changes
which may have a potentially negative impact on manufacturing efficiency. In addition, cost must constantly be optimised and operational margins maintained. Setting up robots, can help achieve these multiple goals!
Fréderic Fréderic Sente, CEO of Desimone, notes based on his experiences : “For us, a robot is a flexible, robust and highly reliable tool requiring little maintenance and allowing fast format changes. Effective implementation of robotic solutions significantly improves the OEE, reduces production costs, as workforce use and can, when linked to an in-line inspection system, also improve the quality of your products.
The installation of robots can provide additional benefits, such as the improvement of sanitary safety. Bacteriologically sensitive products are no longer manipulated by people. Often, the implementation of robots involves optimization of the number of conveyor, resulting in a reduction in energy consumption. Releasing operators from repetitive and sometimes harmful tasks can be seen as a positive contribution to the well-being of workers. Finally, a sensible combination of robots and inspection systems ensures that products are handled properly and that only flawless products are packaged.
DO YOU HAVE A ROBOT PROJECT?
Some examples of do’s and don’ts
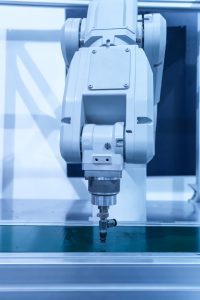
DO’S
1.Determine whether you have sufficient space for the implementation of the robot solution.
2. While calculating the ROI, do not ony take labor recruitment into account but also all other additional elements (there are many).
3. Keep your expectations realistic. Too high unnecessary requirements, for ex speed can make the solution too complex and raise cost.
4. Discuss the design with your supplier and take the time to get the best solution.
5. Analyze problems, failures and errors that occur during production and integrate the solutions in the design. Verify that buffer zones are available so that your line can continue to produce, even if an element of this line stops.
6. Do not forget the up and downstream connections, as well as the potential difficulties associated with it.
7.Keep in mind that operators may, during manual productions, perform corrective actions that cannot be performed with the robot.
8. A successful implementation must be accompanied by thoughtful training for the operators.
9.Remember to link an in-line quality control inspection system to your robot for the rejection of non-compliant products and for the monitoring of the quality performance during production.
10. Choose an independent and reliable partner that is not related to a brand of machines.
DON’TS
1. Base your purchase not only on price. A lower price does not necessarily mean a better return on investment (ROI).
2. Do not suppose that a robot is always the best solution. Sometimes a conventional solution is better suited.
3. Do not start your project without user requirements listing elements such as environmental conditions, product characteristics flexibility requirements, …..,
4. Do not provide a technical solution to the supplier. Let him think for himself. You may be surprised by his creativity!
5. Do’nt be too ambitious for a first project. It’s better to learn to walk before you learn to run.
DON’T BE AFRAID!!
Many companies are reluctant to implement robots because they see them as complex elements for which they have no experience. These companies are therefore likely to fall behind competitors, who are using this technology to build a competitive advantage.
Your fear can quickly be swept away by looking at how other companies use robots. Many companies have already successfully implemented robots, choosing a good partner able to understands their needs. Experience also shows that it is important to involve the various actors at all stages of the project, making the robot technology suddenly seem much simpler.
Another common fear is cost, a robotic solution can be more expensive than a traditional system. Some companies feel that the ROI cannot be realized within the imposed time limit because they limit their cost reduction only on labor.
It is important, however, to quantify the benefits of a robot solution in a wider sense, taking into account additional advantages, such as increased flexibility opening the door to new markets, higher productivity, time saving during production change over, low maintenance costs and longer lifespan. This quickly tilts the balance in favor of a robot solutions.
Conclusion
Robots are the future of the industry. Continuous developments make them always more efficient and flexible. Combined with vision systems and in-line quality control, they increase business profitability, product quality and improve people’s working conditions.